Case Studies
Showcasing some of the products we produced and industries we serviced.
The following are some practical application cases of zinc die casting technology shared with you
- Auto parts: Lock components, handles, seat regulators, etc. of automobiles. Zinc die casting technology can manufacture parts with high precision and complex shapes, meeting the strict requirements of the automotive industry for parts.
- Electronic equipment housings: Such as the housings of tablet computers and smart phones. Zinc die casting can provide strong and aesthetically pleasing protective cases.
- Bathroom hardware: Like faucet handles, shower head components, etc. Zinc die casting products have good corrosion resistance and durability.
- Lighting equipment: Housings and some internal structural components of lamps. Zinc die casting enables the achievement of unique designs and good heat dissipation performance.
- Electric tools: Such as the housings and handles of electric drills and chainsaws. Zinc die casting ensures the strength and comfort of the tools.
- Medical devices: The housings and some components of certain small medical devices require high-precision and hygienic surface treatment.
- Toys: Various complexly shaped toy parts. Zinc die casting can realize rapid mass production and cost reduction.
Zinc alloys advantages
Zinc alloys in die casting allows to develop products and to simplify production, providing a durable end-product. Zinc strength, ductility and stability allows specialists to obtain a better and more resistant product. It is this high ductility that makes zinc ideal for die casting process, in which it is necessary to sustain pressure and expansion without fracturing. Other zinc alloys advantages are used in die casting, such as:
- Electrical and thermal conductivity
- Raw material low cost
- Strong stability, which grants a long-lasting end product with high quality finishing properties
- Thin walls: they contribute to corrosion resistance for end products, increasing their durability in harsh environment
- Economical for small parts
- Low melting point, which means it requires less energy for production
- Dies have a longer tool life
- Complex geometries and quality finishing: by using zinc it is possible to cast intricate, thin walled and technically demanding parts with high precision
- Top quality coating and chrome plating: zinc die casting components are fit for electroplating
Zinc alloy Case Study
Zinc die castings for Bathroom hardware
The application advantages of zinc alloy in the bathroom field mainly include the following points:
- Good casting performance: Zinc alloy has a low melting point and good fluidity. It is easy to be die-cast and can be used to manufacture complex-shaped, thin-walled precision parts. Moreover, the surface of the castings is smooth.
- Easy processability: Zinc alloy has the characteristics of easy fusion welding, brazing and plastic processing, without the need for complex welding and processing procedures.
- Rich product styles: Its high plasticity enables it to be used to manufacture various bathroom products with arcs, curves and shapes, which has a greater competitive advantage in product styles.
- Convenient surface treatment: Surface treatments such as electroplating, spraying and painting can be carried out to obtain a better appearance effect.
- Relatively low cost: Compared with some other materials, the price of zinc alloy is relatively low, which helps to reduce the manufacturing cost of bathroom products.
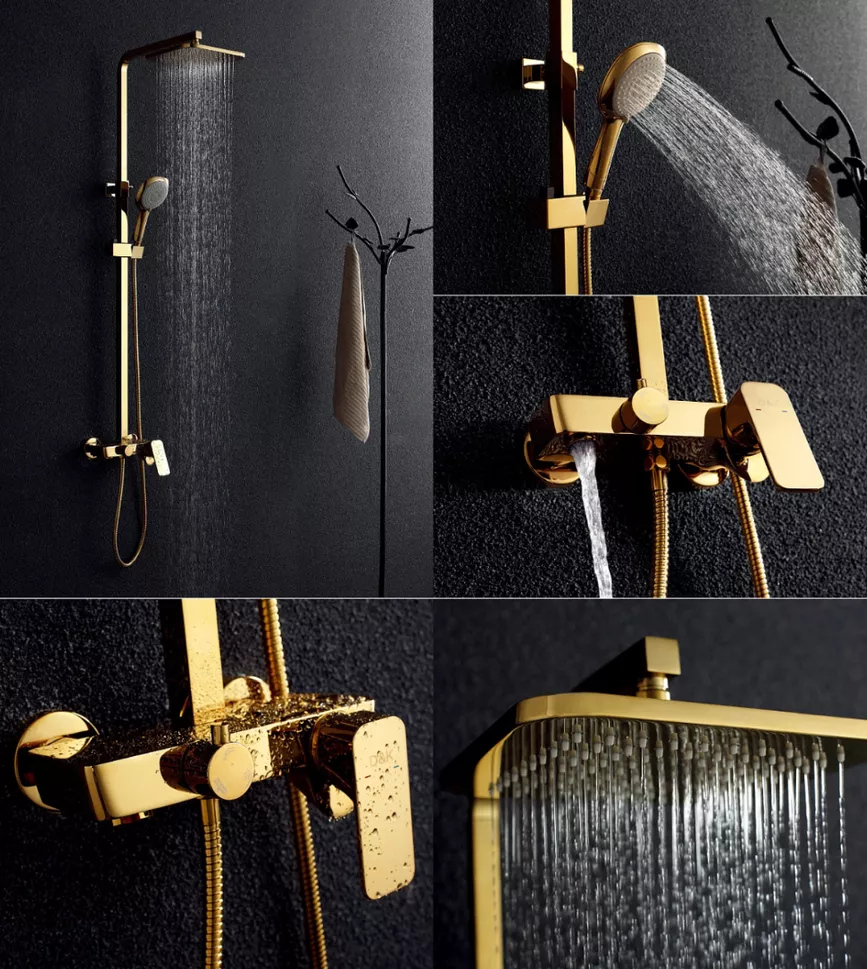
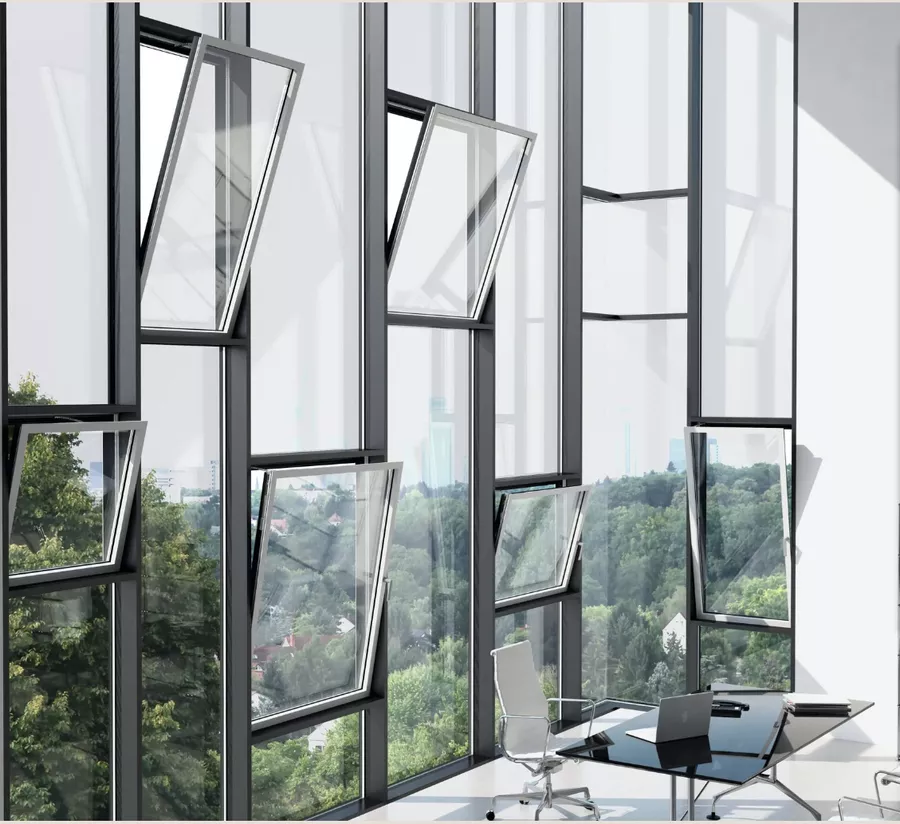
Zinc die castings for Door and Window System
Zinc alloy die casting has certain application advantages in the door and window system.
Firstly, zinc alloy has good casting performance and can produce door and window components with complex shapes and high dimensional accuracy to meet diverse design requirements.
Secondly, the strength and hardness of zinc alloy are relatively high, which can enhance the structural stability and safety of doors and windows.
Furthermore, zinc alloy has good corrosion resistance and can maintain good performance under different environmental conditions, prolonging the service life of doors and windows.
Zinc die castings for Auto Parts
There are several reasons why companies prefer zinc die casting in the automotive industry. Let us explore these reasons one by one in detail.
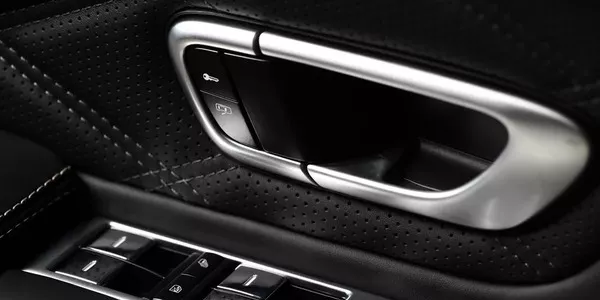
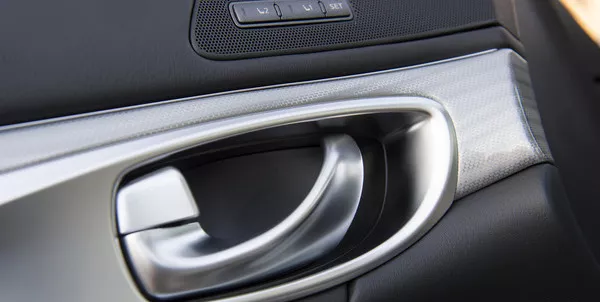
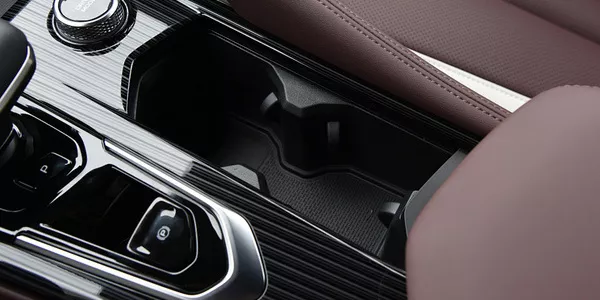
High Strength and Hardness
Zinc die casting components are ideal for the automotive industry due to their incredible strength and hardness.
Die-cast zinc alloys possess the strength to bear the high dynamic and thermal loads automobiles are subject to. Their hardness allows them to survive impact loading and surface wear and tear.
Electrical Conductivity
Good electrical conductivity is a very desirable quality for automotive components housing electrical circuitry. Zinc die castings in automotive applications are becoming increasingly popular due to zinc’s electrical conductivity properties.
Low Costs
Among other metals like aluminum, zinc die casting in the automotive industry is a relatively cheaper process.
Zinc has a lower melting point so it melts quickly, saving energy costs. Its high-pressure die casting method is faster than alternative processes. Hence, higher productivity directly leads to lower production costs.
Dies for zinc die casting also has a longer life. As a result, the overall manufacturing costs are significantly low.
Complex Geometric Features
Zinc alloys in the automotive industry are often used to manufacture complex geometries. The mechanical properties of zinc make it suitable for features with thin walls, curved surfaces, slender parts, thin cross-sections, etc. Modern equipment makes it possible to die cast zinc walls as thin as 0.5 mm.
High Dimensional Tolerance
Zinc die casting is a near-net shape process, boasting a repeatability of +/- 0.001 inch for small geometries. Generally, it beats competing metals like aluminum and magnesium with its compatibility with low-temperature, high-pressure.
Moreover, its higher fluidity is another reason for its superior dimensional tolerance. It fills the die cavity entirely and is, thus, better able to maintain its shape during thermal contraction.
Good Surface Quality
In addition to its aforementioned benefits, it is also responsible for the elite surface quality of zinc die casting in automotive industry.
Zinc’s fluidity allows it to fully fill the cavity, leaving no gaps between the walls and the molten metal, which enables it to fully capture the surface texture in detail. Moreover, it also does not adhere to the mold’s walls. As a result, there is less pitting on the surface, which increases its smoothness a lot.
Furthermore, a common reason for high surface roughness in cast parts is porosity. Casting-induced pores are visible on the surface and make it coarse. As zinc die casting has low porosity, it creates a smooth, pore-free surface.
Additionally, zinc alloys are also compatible with many surface treatment procedures like chrome plating and painting. Such post-processing methods further improve the surface quality of zinc components.
As said before, automotive industry is the most common application of die casting: by using zinc and its alloys is possible to produce components capable of reaching high aesthetic quality , with strict and narrow tolerances for shapes morphology. Zinc alloy is also used for plating purposes because of its many benefits, such as enhancing the already impressive anti-corrosion zinc properties.
Zinc die castings for Medical devices
Zinc alloy die casting has certain applications in the field of medical devices. Compared to traditional metal materials, zinc alloys have some unique advantages.
Firstly, the physicochemical properties of zinc alloys make them suitable for certain medical devices. Compared with titanium alloys or stainless steel, the mechanical properties of zinc or zinc alloys are closer to those of human bones. After preparing zinc alloys by adding elements such as copper, iron, and manganese to zinc metals, their yield strength and ductility are improved, which can meet the material mechanical performance requirements of some medical devices.
Secondly, the standard corrosion potential of zinc alloys is -0.76V. Theoretically, the degradation rate is slower than that of magnesium metal materials, and the degradation trend is more gentle. The degradation rate in 12 weeks is only 9% – 11% (specifically related to the composition of the alloy), and complete degradation generally requires more than 20 months. This slow degradation characteristic can theoretically ensure that the structural integrity is not prematurely lost during processes such as fracture healing, and is closer to the expected requirements for biodegradable metal bone implant materials.
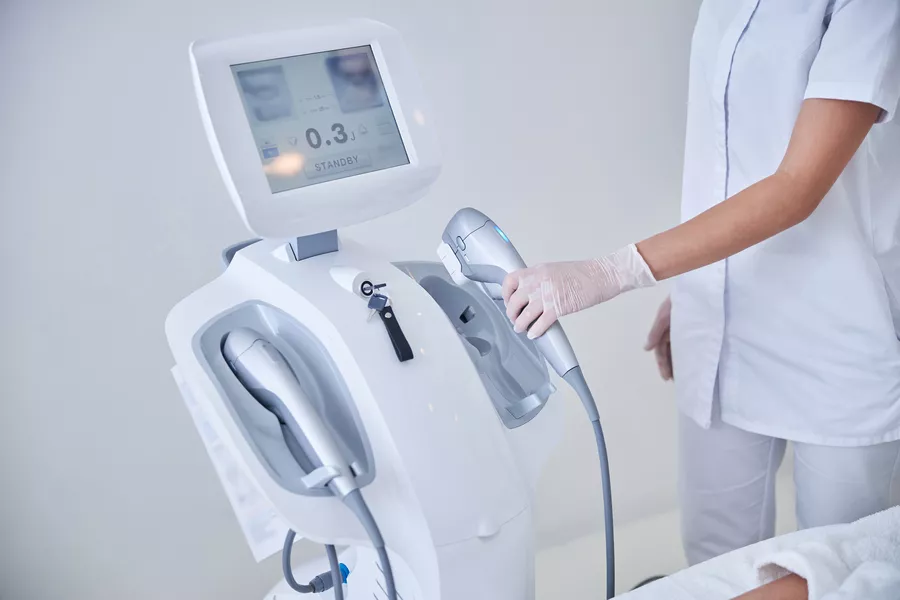
The following provides you with detailed descriptions of some application examples of zinc alloys in the field of medical devices:
In the orthopedic field, zinc alloys can be used to manufacture fracture fixation devices, such as bone plates and screws. Their moderate strength and good biocompatibility help provide stable support for the fracture site and promote bone healing. Moreover, the degradation rate of zinc alloys is relatively slow, enabling them to maintain sufficient mechanical properties during the bone healing process.
In the cardiovascular field, researchers are exploring the application of zinc alloys in the manufacturing of cardiovascular stents. Due to the certain degradability of zinc alloys, compared to traditional permanent metal stents, they can reduce the potential risks caused by long-term retention in the body.
In oral medicine, zinc alloys can be used to make the supports or components of dentures. Their good mechanical properties and corrosion resistance help improve the stability and service life of dentures.
In terms of surgical instruments, for example, the handles or components of certain small surgical tools, the die-casting characteristics of zinc alloys can produce complex-shaped instruments to meet specific surgical operation requirements.
Zinc die castings for Safety Lock System
Zinc alloy die casting is widely applied in the field of safe locksets for the following reasons:
- Sturdy and wear-resistant: Zinc alloy has high strength and hardness, which can meet the requirements of safety and durability for safe locksets.
- Easy to form: It can be die-cast into lockset components with complex shapes, providing more possibilities for design, such as some lock cores and handles with unique shapes or special structures.
- Diverse surface treatments: It can undergo treatments such as electroplating, polishing, oxidation, grinding, blackening, spraying, electrophoretic gold plating, sandblasting, grit blasting, fine polishing, surface anodizing, etc., thereby achieving various appearance effects to meet different aesthetic needs. At the same time, it also helps improve the corrosion resistance of the locksets.
- Moderate price: Compared to materials such as stainless steel and copper alloys, the cost of zinc alloy is relatively reasonable. While ensuring the quality of the locksets, it can also control the production cost.
Many popular traditional safe locksets and trendy intelligent safe door locks on the market are made of zinc alloy. For example, some safe rotary mechanical combination locks made of zinc alloy die casting have shells with moderate strength and good wear resistance, which helps ensure the stability and safety of the combination locks.
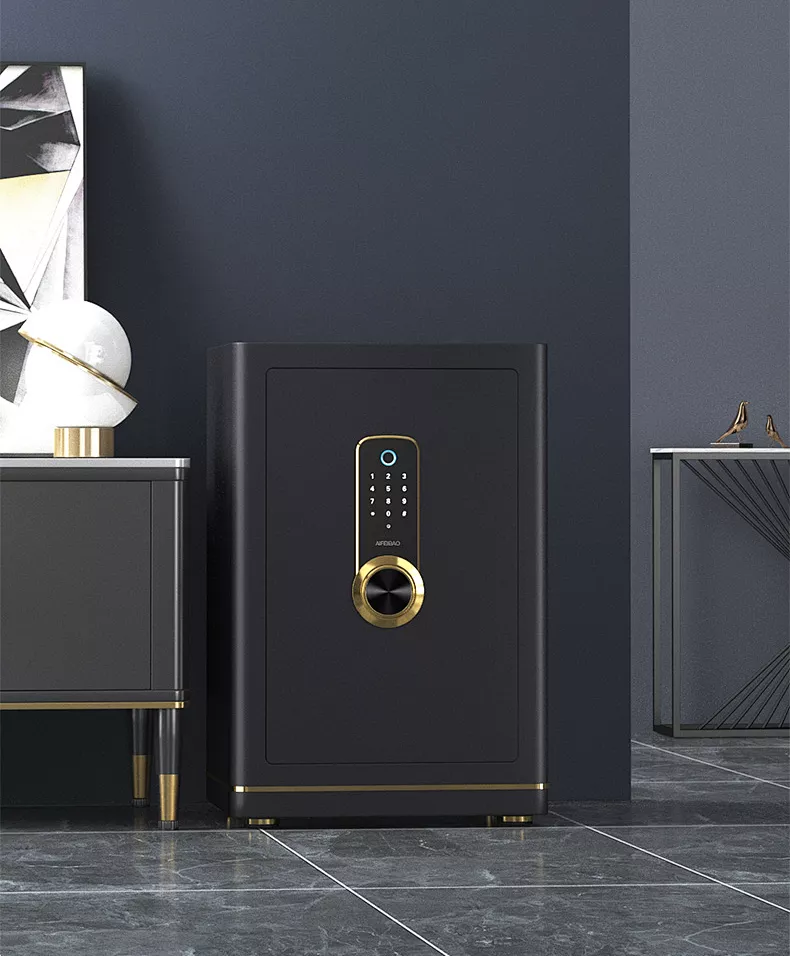
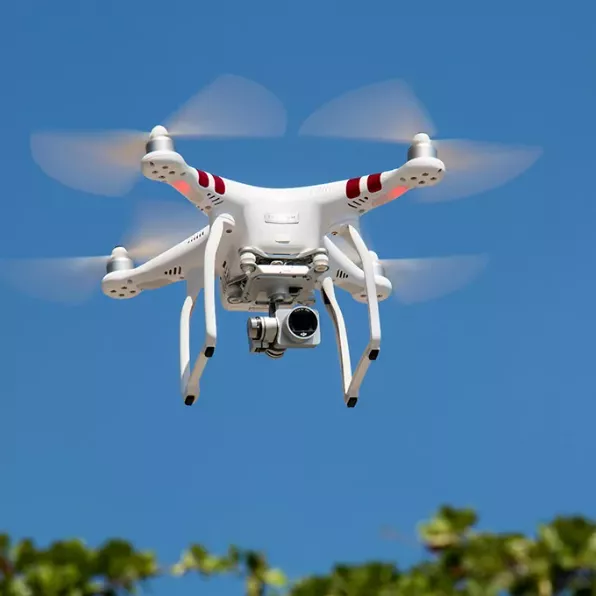
Zinc die castings for Electronic equipment housings
Die casting is used in the electronics industry for its ability to produce complex, highly detailed and accurate metal parts in large quantities. The process creates a uniform and consistent parts with a smooth surface finish which is important for housing delicate components. Additionally, die casting can be used to produce parts with intricate shapes, thin walls and tight tolerances which are often required in electronic applications. The process also offers the option of incorporating internal voids and passages for electrical and mechanical connections.
Zinc die casting and aluminium die casting are used to make electronic products. Zinc die casting is used in applications that require high mechanical strength such as connectors and terminal blocks. Zinc has good castability and can be easily formed into complex shapes making it well - suited for die casting. Additionally, zinc offers good electrical conductivity and good corrosion resistance which are important factors in the electronics industry.
Zinc die casting has emerged as a key player in the electronics industry offering a winning combination of precision, cost effectiveness and superior mechanical properties. As electronic devices continue to advance in complexity and miniaturization, the role of zinc die casting is likely to expand further that will also contribute to the evolution of the electronics landscape. Manufacturers and engineers are embracing this versatile manufacturing process to meet the growing demands for high quality electronic components in the digital age.
Devis rapide
Enough is known about us. Let's talk about your project now.